汽車線束高頻焊接雙絞線,智能駕駛時代的核心連接技術
時間: 2025-02-23 10:38:35 瀏覽次數:80
“一輛現代汽車中,線束總長度超過5公裏,連接著上千個電子元件。” 隨著新能源汽車與智能駕駛技術的快速發展,汽車線束的設計與製造工藝正麵臨前所未有的挑戰。其中, 高頻···
“一輛現代汽車中,線束總長度超過5公裏,連接著上千個電子元件。” 隨著新能源汽車與智能駕駛技術的快速發展,汽車線束的設計與製造工藝正麵臨前所未有的挑戰。其中,高頻焊接雙絞線作為提升信號傳輸質量與抗幹擾能力的關鍵技術,正在成為行業升級的焦點。
一、為什麽高頻焊接雙絞線成為汽車線束的“新寵”?
傳(chuan) 統汽車線束多采用單芯導線或簡單絞合工藝,但在電動化與(yu) 智能化趨勢下,高頻信號傳(chuan) 輸需求激增。例如,自動駕駛係統的毫米波雷達、車載以太網、高分辨率攝像頭等設備,均需要傳(chuan) 輸高頻、高帶寬信號。此時,普通線纜的電磁幹擾(EMI)問題會(hui) 嚴(yan) 重影響信號完整性,甚至引發係統誤判。
雙絞線通過兩根絕緣導線以螺旋方式纏繞,可有效抵消外界電磁幹擾。而高頻焊接技術的引入,進一步解決了傳統絞合工藝中接觸電阻不穩定、焊點易氧化等問題。通過高頻電流產生的局部高溫,焊接過程能在毫秒級時間內實現金屬分子層麵的熔合,形成零縫隙連接,從而確保信號傳輸的連續性與穩定性。
二、高頻焊接雙絞線的核心技術解析
1. 高頻焊接的物理原理
高頻焊接利用電磁感應原理,通過交變磁場在導體(ti) 表麵產(chan) 生渦流,使金屬瞬間升溫至熔融狀態。與(yu) 激光焊接或超聲波焊接相比,高頻焊接的熱影響區更小,且能適應銅、鋁等多種材料的焊接需求。這一特性尤其適合汽車線束中不同材質的導線連接場景。
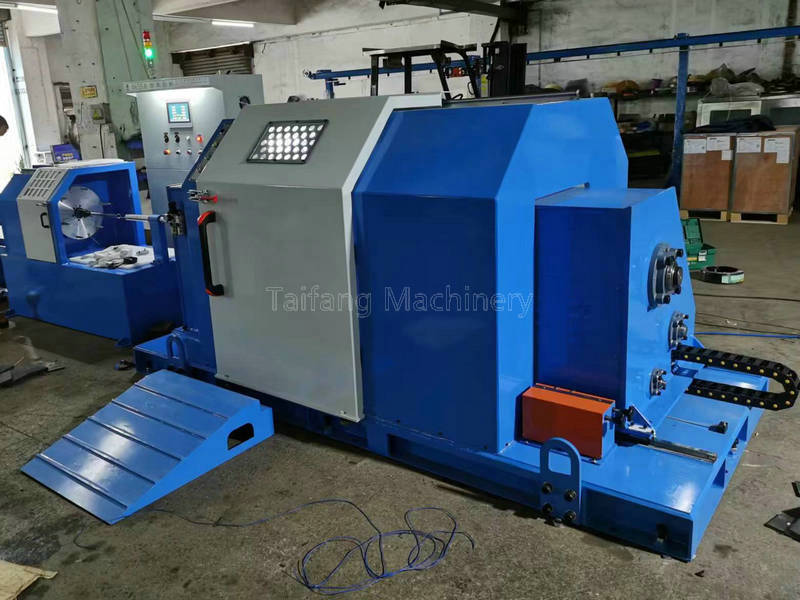
2. 雙絞線設計的工程優化
雙絞線的絞距、絞合角度直接影響其抗幹擾能力。研究表明,當絞距與(yu) 信號波長呈特定比例時,可最大化抑製共模噪聲。例如,在傳(chuan) 輸CAN FD(控製器局域網靈活數據速率)信號時,絞距控製在15-25mm範圍內(nei) ,可將信號衰減降低30%以上。
3. 工藝與材料的協同創新
為滿足汽車行業對輕量化的需求,鋁導體的應用比例逐年上升。然而,鋁的氧化特性使其焊接難度遠高於銅。通過高頻焊接+惰性氣體保護的組合工藝,鋁導體的焊接強度可提升至銅導體的90%,同時降低線束總重量達15%。
三、高頻焊接雙絞線的實際應用場景
1. 新能源高壓係統
在800V高壓平台車型中,電機驅動係統的工作頻率可達20kHz以上。高頻焊接雙絞線不僅(jin) 能承載大電流,還可減少因高頻諧波引起的能量損耗,提升整車能效。某頭部車企的實測數據顯示,采用該技術後,高壓線束溫升降低了12%。
2. 智能座艙與車載網絡
車載信息娛樂(le) 係統(IVI)需要同時傳(chuan) 輸音頻、視頻與(yu) 控製信號。通過屏蔽層+雙絞線的複合結構,高頻焊接技術可將串擾噪聲控製在-70dB以下,滿足4K視頻傳(chuan) 輸的嚴(yan) 苛要求。
3. 自動駕駛傳感器網絡
激光雷達與毫米波雷達的信號頻率高達77GHz,傳統線束的阻抗失配會導致信號反射。采用特性阻抗精準控製的高頻焊接雙絞線,可將電壓駐波比(VSWR)優化至1.5:1以內,確保傳感器數據的實時性與準確性。
四、行業趨勢與挑戰
根據*Grand View Research*的數據,2023年全球汽車線束市場規模已突破500億(yi) 美元,其中高頻線束的複合增長率達18.7%。然而,技術升級仍麵臨(lin) 兩(liang) 大挑戰:
- 成本與性能的平衡:高頻焊接設備的一次性投入較高,需通過規模化生產降低邊際成本;
- 標準化進程滯後:不同車企對高頻線束的測試標準存在差異,亟需建立統一的行業規範。
新材料的應用正在打開新空間。例如,采用聚四氟乙烯(PTFE)絕緣層的雙絞線,可在-40℃~200℃環境下保持性能穩定,完美適配熱管理要求更高的固態電池車型。
—
通過上述分析可見,高頻焊接雙絞線不僅是汽車線束製造的技術革新,更是智能網聯汽車發展的基礎支撐。隨著5G-V2X、域控製器等技術的普及,這項“隱形”工藝的價值將持續釋放。
TAG: