全自動雙頭端子絞線機,線束加工行業的效率革命
時間: 2025-02-20 23:43:55 瀏覽次數:85
在工業自動化高速發展的今天,線束加工作為電子、汽車、新能源等領域的核心環節,其精度與效率直接關係著產業鏈的運轉速度。 傳統的手工絞線、單機分步加工模式已難以滿足現···
絞線機-的出現-不僅顛覆了行業作業邏輯-更以-雙工位同步處理-與-智能化控製-為核心優勢-成為線束加工領域降本增效的關鍵設備">在工業自動化高速發展的今天,線束加工作為電子、汽車、新能源等領域的核心環節,其精度與效率直接關係著產業鏈的運轉速度。 傳統的手工絞線、單機分步加工模式已難以滿足現代製造業對規模化、標準化生產的需求。而全自動雙頭端子絞線機的出現,不僅顛覆了行業作業邏輯,更以“雙工位同步處理”與“智能化控製”為核心優勢,成為線束加工領域降本增效的關鍵設備。
絞線機的工作原理">一、全自動雙頭端子絞線機的工作原理
全自動雙頭端子絞線機是一種集送線、剝皮、絞合、壓接、檢測於(yu) 一體(ti) 的高精度設備。其核心設計在於(yu) 雙頭同步作業(ye) 係統:通過兩(liang) 個(ge) 獨立工位同時完成線材兩(liang) 端的端子加工,實現“一機雙產(chan) ”的效果。
設備采用伺服電機驅動技術,能夠精準控製線材長度、絞合圈數及壓接力度,誤差可控製在±0.1mm以內。同時,內置的視覺檢測模塊可實時識別端子壓接質量,自動剔除不良品,確保成品率超過99.5%。這種“加工-檢測-分選”閉環流程,大幅降低了人工幹預需求。
二、設備的核心優勢解析
1. 效率提升:雙工位設計的倍增效應
傳(chuan) 統單頭設備需逐端加工線材,而雙頭機型通過同步處理線材兩(liang) 端,使生產(chan) 效率直接翻倍。以加工1米長的雙頭線束為(wei) 例,單台設備每小時產(chan) 量可達1200-1500條,比人工操作快20倍以上。
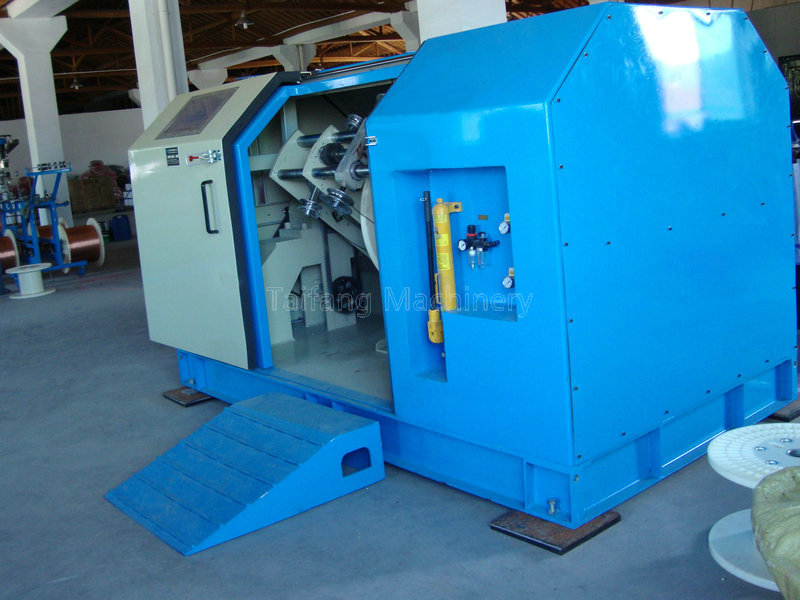
2. 精度保障:智能控製係統的技術突破
設備搭載的多軸聯動控製係統,可針對不同線徑(0.08-6.0mm²)、端子類型(U型、旗型、環形等)自動調整參數。例如,在汽車線束加工中,設備能精準區分0.35mm²的信號線與(yu) 4.0mm²的電源線,避免因參數錯誤導致的接觸不良風險。
3. 柔性生產:快速換型的靈活性
通過模塊化模具設計與配方存儲功能,操作人員可在5分鍾內完成不同產品的切換。這一特性尤其適用於小批量、多批次訂單,幫助企業在定製化需求中保持競爭力。
三、典型應用場景與行業價值
1. 汽車製造:高可靠性的核心需求
現代汽車線束包含超過5000個(ge) 連接點,傳(chuan) 統工藝的誤差率可能導致整車電路故障。全自動雙頭端子絞線機通過恒壓壓接技術(如CRIMP力監控),確保每個(ge) 端子接觸電阻穩定在5mΩ以下,滿足ISO 6722車用線束標準。
2. 新能源領域:大線徑加工的技術挑戰
在光伏接線盒、儲(chu) 能電池包等場景中,設備可處理6.0mm²以上的粗線纜,通過液壓壓接單元實現3000N以上的壓接力,避免大電流場景下的端子脫落風險。
3. 消費電子:微型化趨勢下的精度考驗
針對Type-C接口、FPC排線等微小型端子(最小0.8mm間距),設備通過高分辨率CCD相機與微米級送線機構,實現精準對位,將加工公差控製在±0.05mm內。
四、選購設備的實用指南
企業(ye) 在選擇全自動雙頭端子絞線機時,需重點關(guan) 注以下維度:
- 兼容性:確認設備支持的最大線徑、端子類型與模具接口標準(如JAM、TE標準)
- 穩定性:伺服電機品牌(如安川、鬆下)與導軌精度(建議選擇HIWIN線性導軌)
- 擴展性:是否預留物聯網接口,支持MES係統數據對接
- 能耗比:比較不同型號的功率消耗(通常單機功耗≤3kW)與產能比值
值得注意的是,部分高端機型已集成AI缺陷分析功能,通過機器學習自動優化壓接參數,長期使用可降低15%以上的材料損耗。
—
通過上述分析可見,全自動雙頭端子絞線機不僅是簡單的效率工具,更是推動線束加工行業向智能化、標準化、零缺陷生產轉型的核心動力。隨著5G通信、智能汽車等新興領域的爆發式增長,這類設備的市場滲透率預計將在未來三年內突破40%,成為高端製造領域的標配裝備。
TAG: